Discover the Stories behind Leading Products
Talks of our scientists, engineers and product developers
who thrive on the challenge of creating and designing new products
STORY 01The story behind SELAPath,
An Oxide Solid Electrolyte for Lithium-ion Secondary Batteries
An Oxide Solid Electrolyte for Lithium-ion Secondary Batteries

* This oxide crystal is represented by the chemical formula Li1.4Al0.4Ti1.6(PO4)3 (LATP).
LATP has been known for a long time as a solid material that can conduct lithium ions, and since the 1990s, Sumita has been researched the production of LATP synthesized from glass and exploring the ways to utilize it. Since that time, Sumita has been studied whether it can be used as a solid electrolyte for lithium-ion secondary batteries.
Sumita Optical Glass’ engineer talks about the story behind SELAPAth development, its characteristics, and his work.
How SELAPath was developed
How did you start working on the battery material, SELAPath?
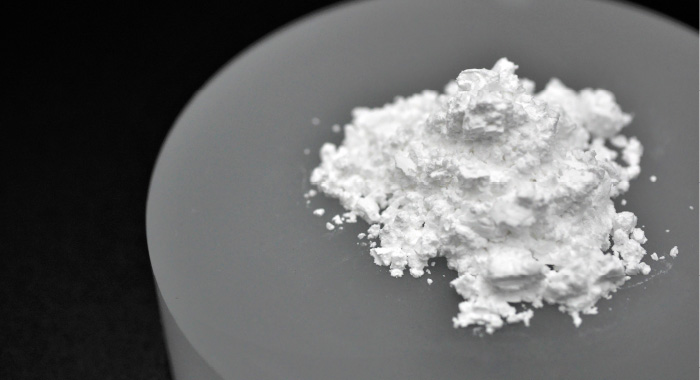
Shortly after I started working at Sumita, I took over the R&D project of battery material using LATP from my supervisor. The glass composition I developed happened to work well, and I began to work on this project intensively. At the time, battery fire and explosion incidents attracted attention to the issue of battery safety as well as all-solid-state batteries that use non-flammable ceramics as the electrolyte.
Did the development of the battery material go smoothly?
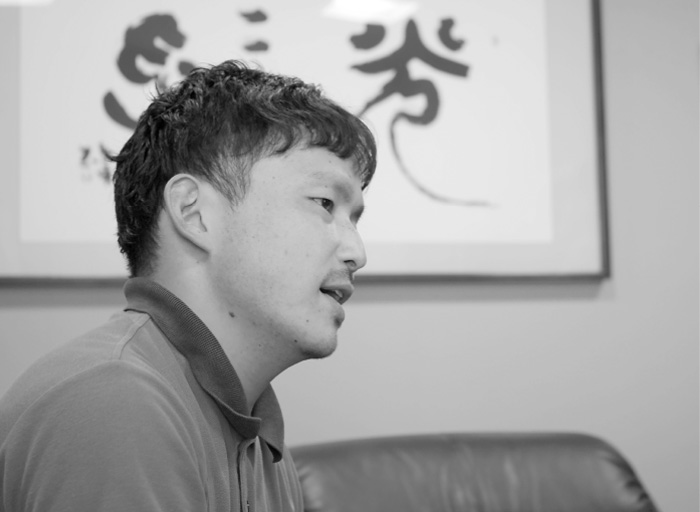
The glass composition of the material was not so difficult, as I only had to change the composition of the existing materials. The challenge was in the scale-up process. Scale-up processes are frequently non-linear. Even factors that do not affect the quality in small-scale production, such as laboratory level, can cause problems in large-scale production. The most difficult part for us was establishing the scale-up process to deliver consistently high-quality material, and it still is. This is what we keep paying close attention to, to ensure delivering consistent quality even for large scale production. Thus, with regard to SELAPath, what I have been focusing on was its process development.
What exactly was the challenge of process development?
SELAPath is made using Sumita’s original manufacturing method, aka “Glass Crystallization Method” (patent pending), by synthesizing LATP from specialty glass. The basic manufacturing method of SELAPath and our general optical glass is the same but differs in some processes. Also, the furnaces and environment for manufacturing SELAPath are different from those used in laboratory-level and small-scale prototyping for mass production.
For a large scale production, we dealt with issues one by one by verifying each process with production staff, the process including melting conditions. I won't go into the details of the manufacturing process as it relates to expertise in glass manufacturing and a detailed understanding of the nature of the material.
What allows Sumita to provide large-scale production of SELAPath?
Sumita has been selling LATP-Ag (antimicrobial agent) since the early 2000s when the demand for antimicrobial agents increased, and for that reason, Sumita had received inquiries from customers about the possibility of using LATP as a battery material. This helped us to establish the manufacturing process of SELAPath and prepare facilities for large-scale production. I was fortunate that I worked on a project that requires mass production from the early stage of development. This experience taught me the importance of putting myself in the customer's shoes and considering commercial production from the beginning. In the other projects I am currently working on, I begin with the customers’ end in mind, including large-scale productions, while developing materials.
Features of SELAPath
Please tell us about what differentiates SELAPath from other battery materials.
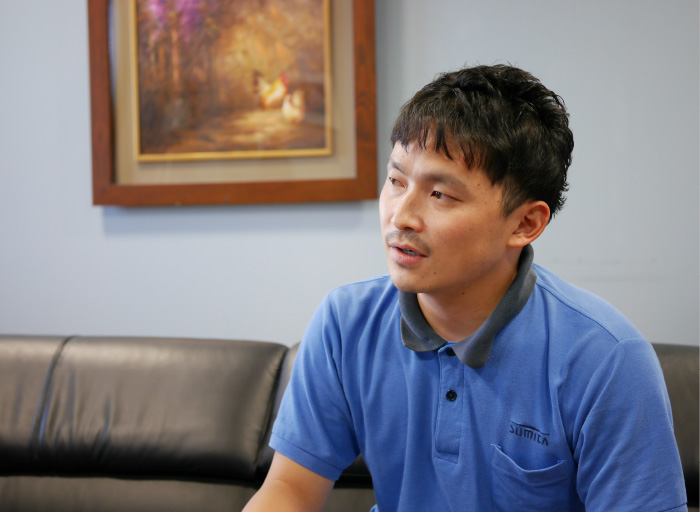
The biggest advantages of this material are scalability and price competitiveness. Our capability of SELAPath with existing facilities is about 150 kg/month, and in case we increase manufacturing capacity, it will be 1 ton/month. I don't think there are other manufacturers capable of this level of production at this time.
The other advantage is its ease of handling and safety. Since the material itself is not new, it does not have particularly high performance in terms of ionic conductivity. However, when considering the spread of a certain product or technology in the market, not only its quality but other factors matter. Material’s difficulty in handling or its high cost which is beyond the market’s acceptance can become bottlenecks. For the practical application and spread of new products/technologies, including all-solid-state batteries, it is important that the cost satisfies the market, regardless of which material is used. In this respect, SELAPath is easy to handle and can be produced on a larger scale at low costs, which are significant advantages in terms of the practical application and diffusion of our customers' products.
What did you mean by [some materials are] “difficult to handle”?
Taking solid electrolyte materials as an example, there are some materials with high ionic conductivity, but require advanced equipment because they cannot be handled in air and have low water resistance as well as the risk of generating toxic gas. In contrast, as SELAPath (LATP) is an oxide, it can be handled safely in air and is easier to handle than sulfide.
What are other features of SELAPath?
In terms of quality, our manufacturing method which does not require a ball milling process allows SELAPath of highly uniform particle shape without ball-milling contaminants.
- SELAPath Particle Shape
- Compared to the traditional manufacturing method (Solid Phase Method), SELAPath manufactured by Sumita’s method (Glass Crystallization Method) has the following features:
- Highly uniform in particle shape
- No ball-milling contaminants are contained due to our distinct manufacturing method that does not require a ball milling process
Is other particle forms of SELAPath available?
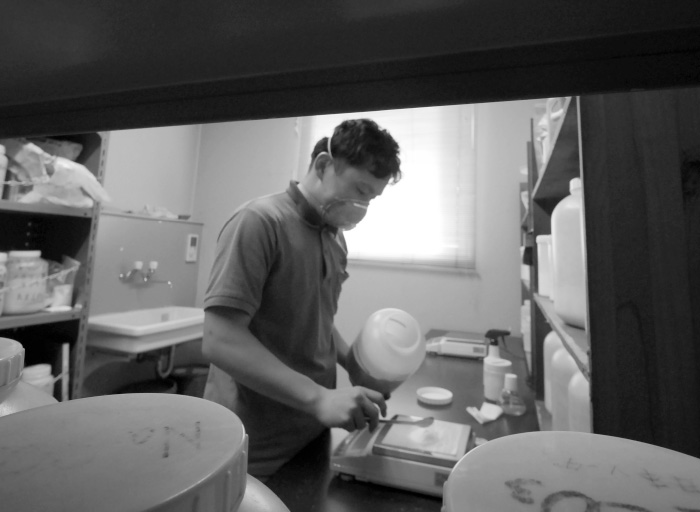
The basic form of standard SELAPath we provide is powder. Particle size can be controlled to some extent. The composition also can be fine-tuned upon customers' request. In addition, Sumita provides contract manufacturing and glass melting services of optical glasses and battery materials using our facilities to customers with needs of large-scale production.
Which specific customers do you think will benefit from SELAPath?
We started promoting SELAPath as an all-solid-state battery material but would like SELAPath to be used not limited to all-solid-state batteries and other batteries but also other usages. This material may be solutions for some completely different purposes that we just don't know. Our position of this material is, "We have developed this material, and established its manufacturing method and system that allow large production at a low price. If you are interested, we hope you try the material for your business problems to be solved." We hope customers make the most use of the material. We would be very happy if we could address customers’ problems and support their business growth with this material and our expertise.
R&D at Sumita Optical Glass
How do you choose your R & D projects?
There are two approaches when we choose projects. One is from ourselves, the other is from customers. The latter approach taught us the specific needs for materials, the needs which we cannot tell by ourselves. The clearer the problem, the easier it is to solve, and if we solve the problem, the more chances of customers use the material. I believe both are important, and we should have both.
What is the most fulfilling part of your job working as a Material R&D Engineer?
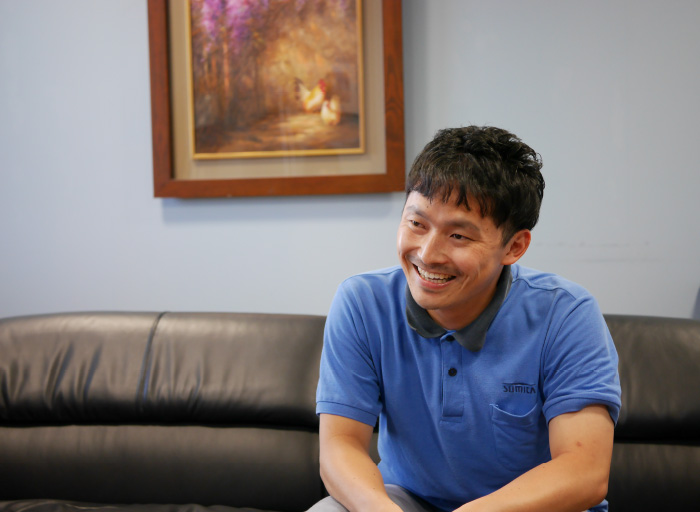
I find it very fulfilling when developed materials are used, incorporated into customers’ products. It is a great pleasure for me when developed materials see the light of day.
What are you currently working on and what are your future goals?
I am mainly working on the development of optical glass. Since Sumita Optical Glass started as an optical glass company, I have been constantly engaged in it. Recently, LATP-related material has become a large proportion of my work, and I am developing new LATP-related materials and working to improve the properties of the material furthermore.
Glass crystallization technology is deep and has more potential. There is a vast reservoir of knowledge regarding the technology to be explored. As I continue my research, I am getting a clearer sense of glass composition and crystallization process in glass crystallization technology. I believe there are optimal combinations of material and process depending on a design that you would like to deposit in the end, such as crystalline material type, its amount and size, as well as its composition and heat treatment process. Selecting the proper combination leads to the subset which best matches the request of a design.
I would like to utilize and apply the technology to other applications. I hope to develop materials that will be widely used and to be adopted as de facto standards such as K-VC89 (lens material for telecommunications).
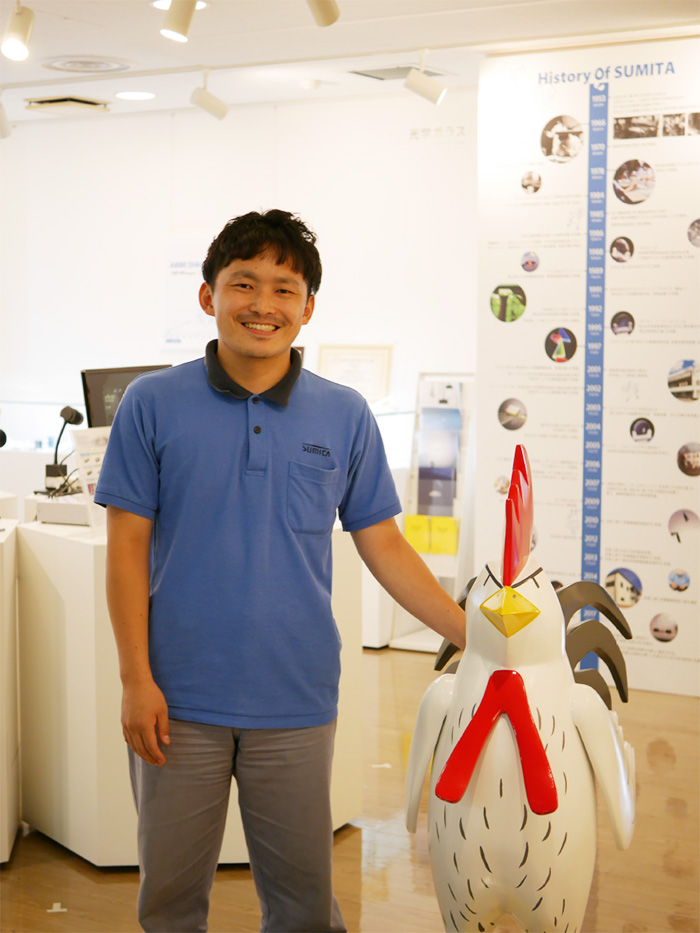